COMPOSITE
Explore our selection of high-performance composites materials and special coatings. Find out how composites hold the solution for your next project: from acoustic performing flexible panels to coating that can simulate ceramics or carbonised wood.
- RAMSAY GROUP -
COMPOSITE
Composite materials allow architects and designers enormous freedom of design. This durable, robust, lightweight and low maintenance material can be produced with an almost limitless array of surface finishes. Roofs, façades, floor and wall coverings, domes, shading elements and other architectural structures are all applications where the unique properties of composite materials can provide enormous benefits.
The composite manufacturing process varies according to materials and desired output for the final composite material. The three main composite manufacturing processes are open moulding, closed moulding and cast polymer moulding. Then there are a variety of processing methods within each of these. Which composite manufacturing methods are used is a decision made according to the material, design and application of the final composite.
CLOSED MOULDING
Closed moulding composite manufacturing processes involve creating parts or products in a closed or sealed mould, providing a controlled environment for the curing or solidification of the composite materials. This process offers advantages like precise material control, higher fibre volume fractions, improved mechanical properties, reduced emissions, and suitability for producing complex parts.
LETS WORK TOGETHER.
If you have an idea, concept, technical design or would like to learn more about our architectural products, please contact us.
COMPRESSION MOULDING
Ideal for fairly small products needing fully moulded geometry, compression moulding can be done with either thermoset or thermoplastic resins as well as a wide range of different fibre types and lengths. The process itself sees a charge of fibre and resin placed into a preheated mould which is closed and kept under pressure until the resin has cured. A Class A surface finish can be achieved which has seen this composite manufacturing method applied to the automotive industry in particular.
INJECTION MOULDING
Injection moulding is arguably the most widely used net-shape manufacturing process for composite materials. Bulk moulding compound is heated before being injected into a heated mould where it is held under pressure until the resin has cured.
Used primarily for fairly small components, injection moulding can mass produce high precision parts requiring specific geometry at a low cost. As advances are made in the composites manufacturing and design process, more and more materials are being used in injection moulding to meet the increasing demand for varying plastic products.
AUTOCLAVE CURING
This is a closed moulding composite manufacturing tool which uses pressurised steam to perform a range of processes. By creating a high pressure environment inside the autoclave, it is possible to produce accurate results with the desired fibre content. The process itself involved curing raw materials inside a two sided mould or, in some instances, a deoxygenated vacuum bag. Both processes are able to produce large quantities of material which makes this a highly suitable process for large facilities.
Autoclave curing guarantees consistent polymer hardening which makes it excellent for manufacturing composites. After applying a release gel on to the moulds surface, fibre textiles are placed into the mould, these are prepregs so have already been saturated with resin.
BRAIDING & WEAVING
Braiding and weaving are narrow width textile composite manufacturing methods. It is a highly suitable method for developing seamless cylindrical textile reinforcement for developing composite structures and as a fast manufacturing process with reduced wastage, it is the perfect composite manufacturing process for numerous items.
Incredibly strong braided composites are known for their superior toughness and durability, particularly when compared to filament wound composites. They are used in a range of braided fabrics and can be created with a number of configurations using carbon, glass, aramid and hybrid fibre systems.
OPEN MOULDING
Open moulding composite manufacturing processes involve creating composite parts in an open mould, allowing for easy access to the mould and direct application of composite materials. Unlike closed moulding processes where the mould is sealed, open moulding processes are more straightforward and typically result in parts with less precise control over material distribution. This manufacturing process is often used for production parts with lower tooling costs, faster production times, and simplicity in design.
Composite In Use . . .
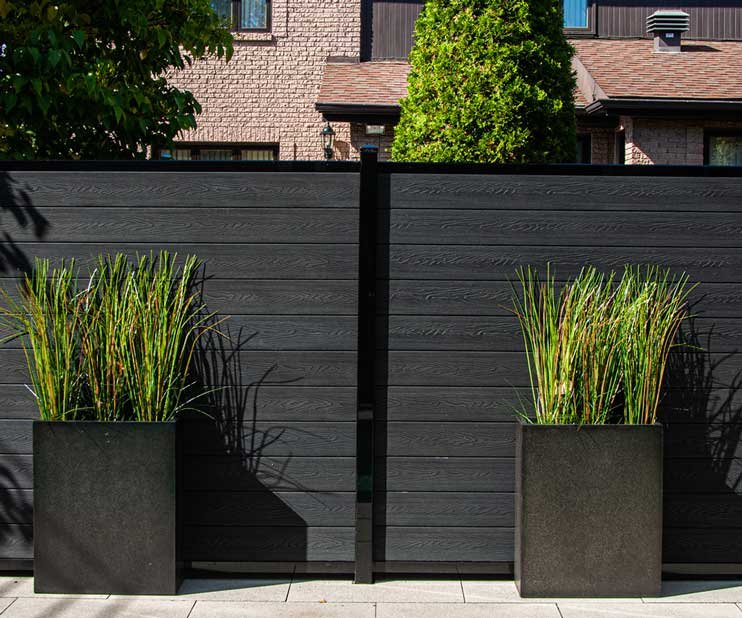
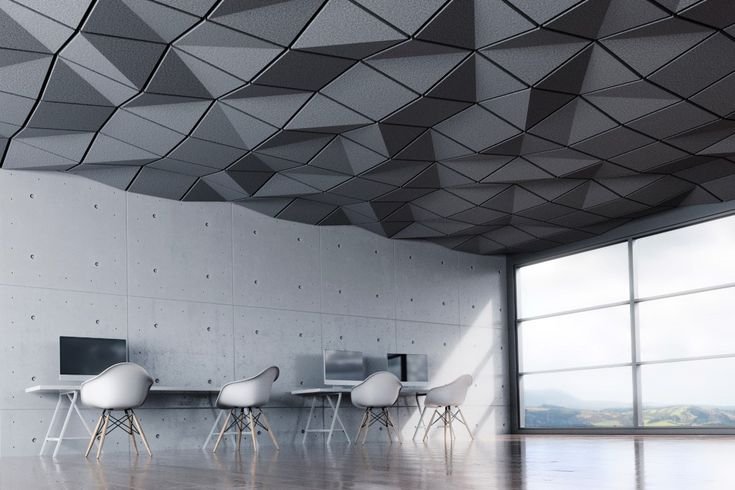
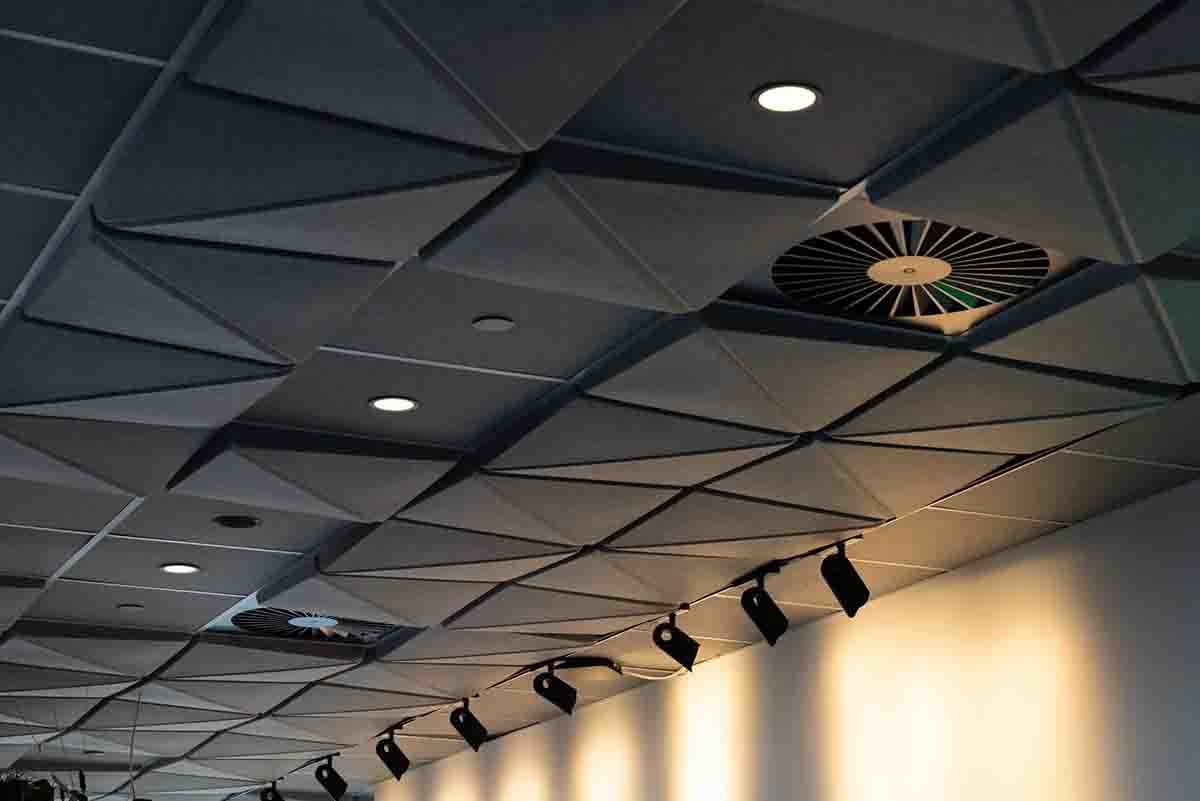
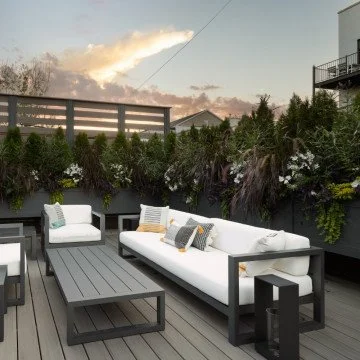
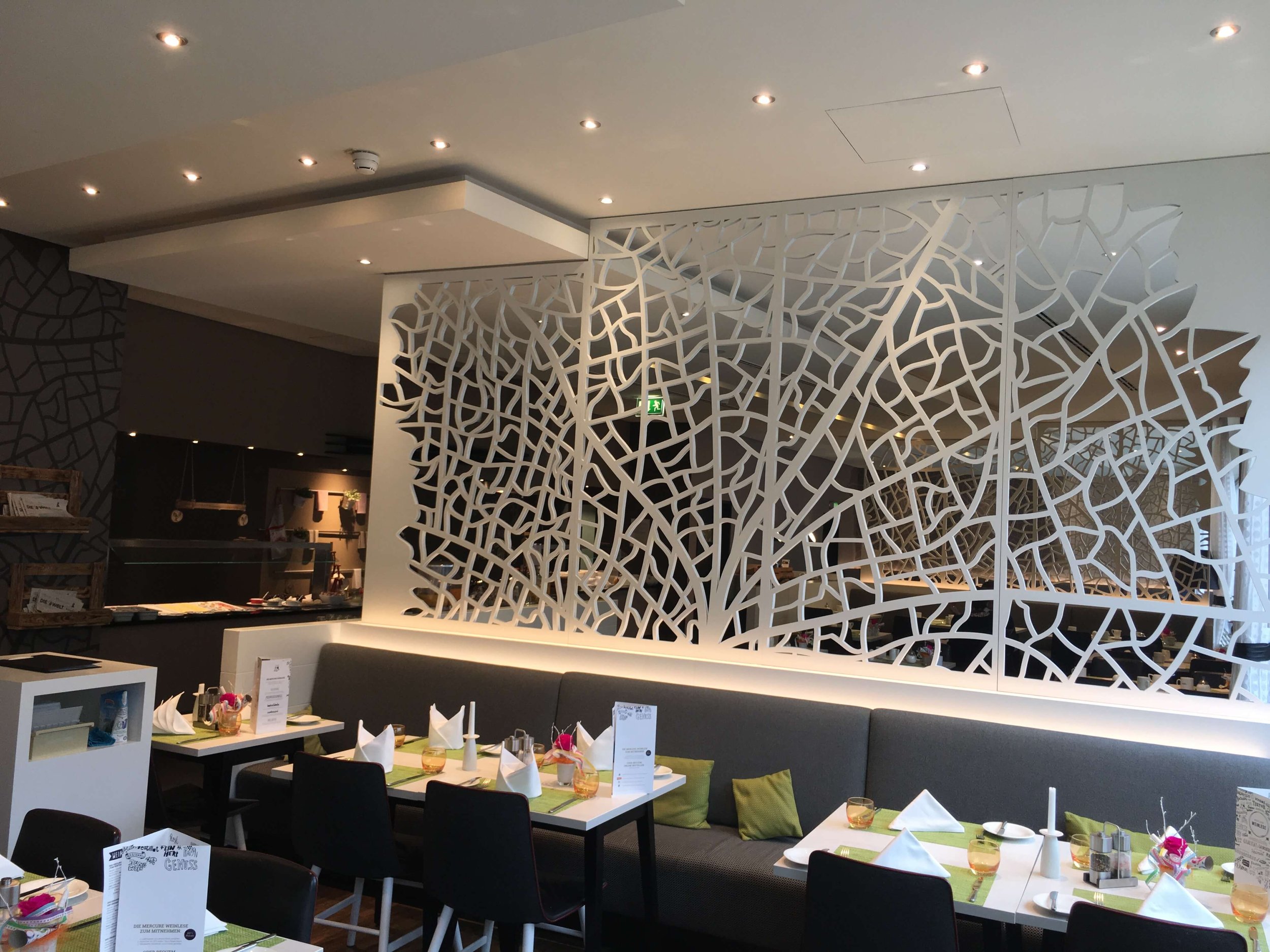
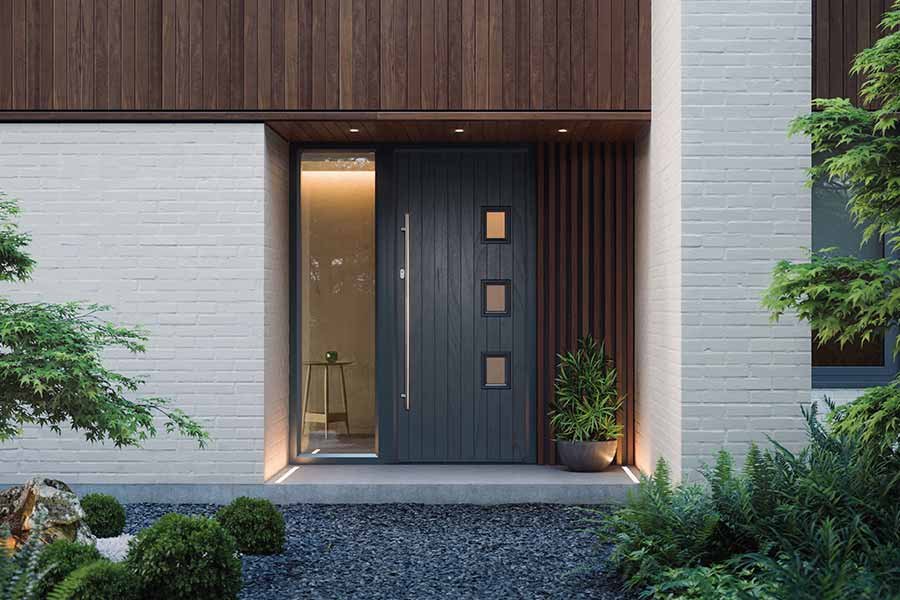

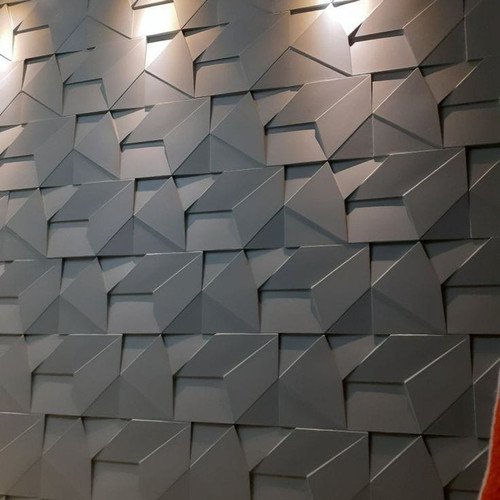
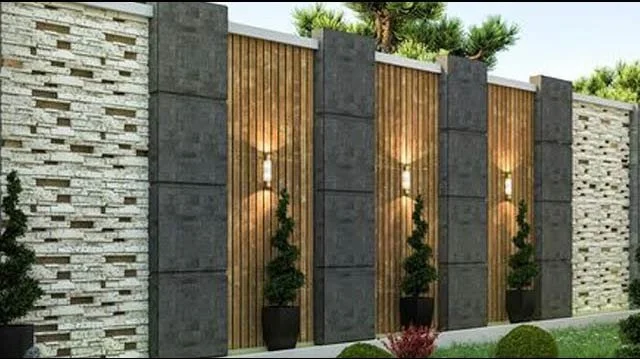